Cane (Calamus rotang) Products
The raw material used for making the cane product is Pirambu. Based on the size, it is of two types.
The artisans got the long size pirambu from the wholesale market in Chennai and the small size pirambu is locally available in Manampattu, (Kollidam area) Nagapattinam Dist. Long size pirambu is used for outlining (designing) i.e. frame work and the small size pirambu is used only for the binding, filling and joining work. The length of the pirambu varies from 11-17 feet.
Cost of the long size Pirambu: Rs. 3500-4000 / 100 Nos
Similarly the small size Pirambu: Rs. 400/100 Nos Steps involved in cane product making
-
Peeling
By using small knife, the outer skin is peeled off. The knife has specifically designed for this purpose.
-
Kanu Aadithal
The nodes of the pirambu are removed by using big size knife. Now, the outer skin of the pirambu will get smooth surface.
Labour charge: Rs.40/day
Work done: 100 splits / day / men
-
Soaking and Drying
The pirambu are soaked in water for overnight. Next day morning, it is taken out from the water and dried in shade for one day.
-
Pirambu valaithal
Two iron rods are oppositely fixed on the ground. The length of the iron rod is 1-1.5 feet. The gap between two rods 20 cm. Pirambu piece is kept in between the iron rod and kerosene lamp is lighted and placed nearer to the pirambu piece where the pirambu is to be bent. Due to the heat, piece is melted slowly. At that time, the bending is done by manually. Then the piece is immediately soaked into the water for 15-30 minutes to retain curved or bent postition. Otherwise it will come to normal position.
-
Joining and binding work
Based on the shape of the products the pieces are designed separately. Next the pieces are atttached by small size pirambu pieces. The pieces are joined by using 2-2.5 inch nail and small hammer. The hammer is made out of iron. The length is 25-30cm. The extra pieces are cut by using small size knife.
-
Varnishing
The final step is varnishing. After completion of varnishing the product has shiny surface and attractive look.
Based on the products, labour charges and work done/day are varied. It is given in the tabulated form below.
Items |
Labour required |
Labour charge |
Work
done / day (numbers) |
Cost of the product
(Rs) |
Frame work
(Rs) |
Designing
(Rs) |
Varnish work (Rs) |
Cot |
3 |
250 |
200 |
15 |
2 |
2500 |
Sofa set |
3 |
300 |
450 |
20 |
2 |
3500 |
Unnjel |
2 |
26 |
40 |
3 |
20 |
450 |
Cradle |
2 |
15 |
13 |
2 |
30 |
250 |
Stand unnjel |
2 |
55 |
45 |
3 |
6 |
750 |
Delux racking chair |
2 |
25 |
20 |
3 |
4 |
800 |
Lady rackin chair |
2 |
30 |
20 |
3 |
4 |
800 |
Dinning table |
3 |
40 |
30 |
10 |
5 |
2500 |
Shelf |
2 |
80 |
150 |
15 |
2 |
1400 |
General profile of the ITK holder
Name and address |
: |
Th. Nagarajan
Thaikkal
Sirkazhi Taluk
Nagapattinam District |
Age |
: |
39 years |
Occupation |
: |
Cane product making + Farming |
Experience |
: |
25 years |
Traditional Mud Pot Making
Th.Govindaraj, 60 years old who is residing at Thiruvenkadu village of Sirkazhi taluk in Kanchipuram Dit. He has been practicing traditional mud pot making for about 40 years.
Steps in pot making
River sand is dried for one day.
After drying, it is soaked in water for half day
The sand is mixed with clay at 3:1 ratio
This mixture is manually pressed by using human legs, until it come to colloidal condition
This clay mixture is kept over the wheel.
Wheel is rotated by using wooden stick (Kazhi). (Rotating speed is depends on the skill of the person; wheel cost Rs.500)
After rotation, the mud pot will get full shape except the bottom portion.
The left hand with ash coated cylindrical stone is kept inside the pot and right hand hold the wooden palakai. And pressing is done by using two hands simultaneously. (Wooden palakai made out of Puvarasu tree (Thespesis babulnia). Cost is Rs.20)

Cost of the production: Rs.8/ pot
Sales rate: Rs.10 / pot. |
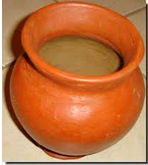 |
Coloured pot |
Source:DSIR, Madurai
|